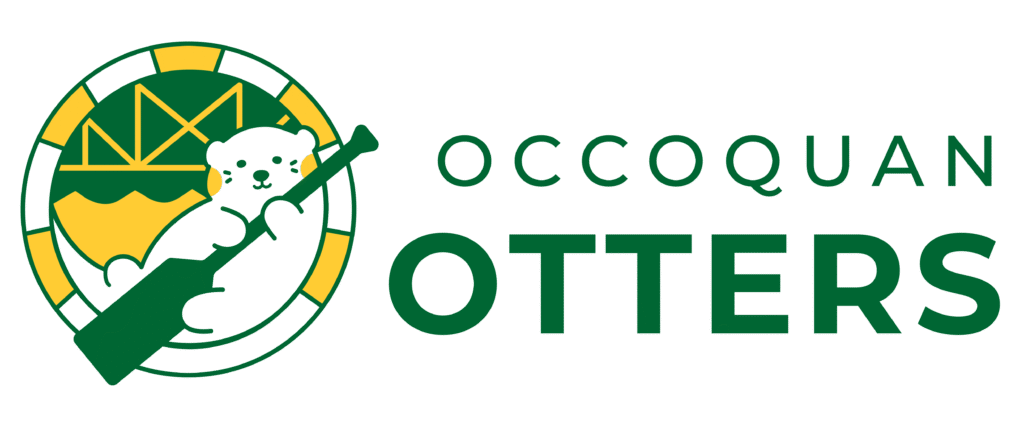
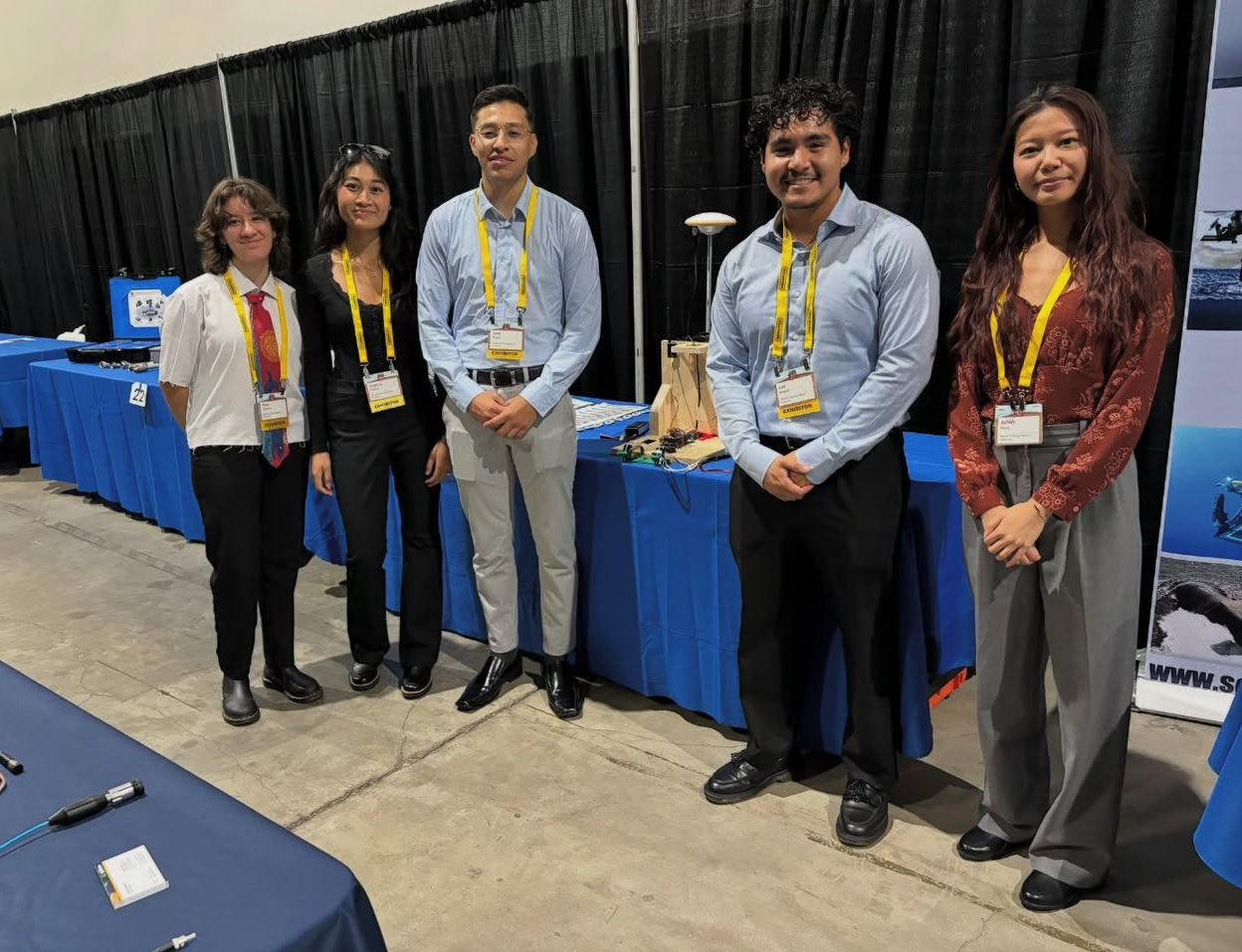
were required to develop an Autonomous Surface Vehicle (ASV) to navigate challenging missions in complex environments with the goal of being competition-ready for RoboNation’s RoboBoat Challenge.
The five senior mechanical engineering students on this team were a part of the student organization RobotX, competing in Sarasota, Florida at the 2024 Maritime RobotX Challenge, where they worked on an autonomous maritime system utilizing a Wave Adaptive Modular Vehicle (WAM-V) platform. The team left a lasting legacy by being the first in George Mason’s history to use the WAM-V platform at a RobotX Challenge. They were also presented with a Systems Engineering Special Award. Dedicating their first senior capstone semester mainly to RobotX, the team has now formed a capstone project committed to building a platform suitable for the ‘sister’ competition, RoboBoat. They tied for 3rd place out of 21 capstone team projects voted and judged by GMU mechanical engineering faculty and staff.
Approach
The Occoquan Otters’ goal is to develop a fully autonomous surface vehicle (ASV), which includes designing and constructing an adequate vessel body that meets competition requirements. The team has worked with Computer Aided Design (CAD), 3D printing, hydrostatic modeling, stability analysis, and electrical work for their capstone project. The RoboBoat will be passed on and used in future competitions by the Plunge Robotics club at George Mason University. There, it will compete
against teams across the globe in autonomous challenges. The Occoquan Otters team is based at the Mason Potomac Science Center in Woodbridge, VAoverlooking the Occoquan River.
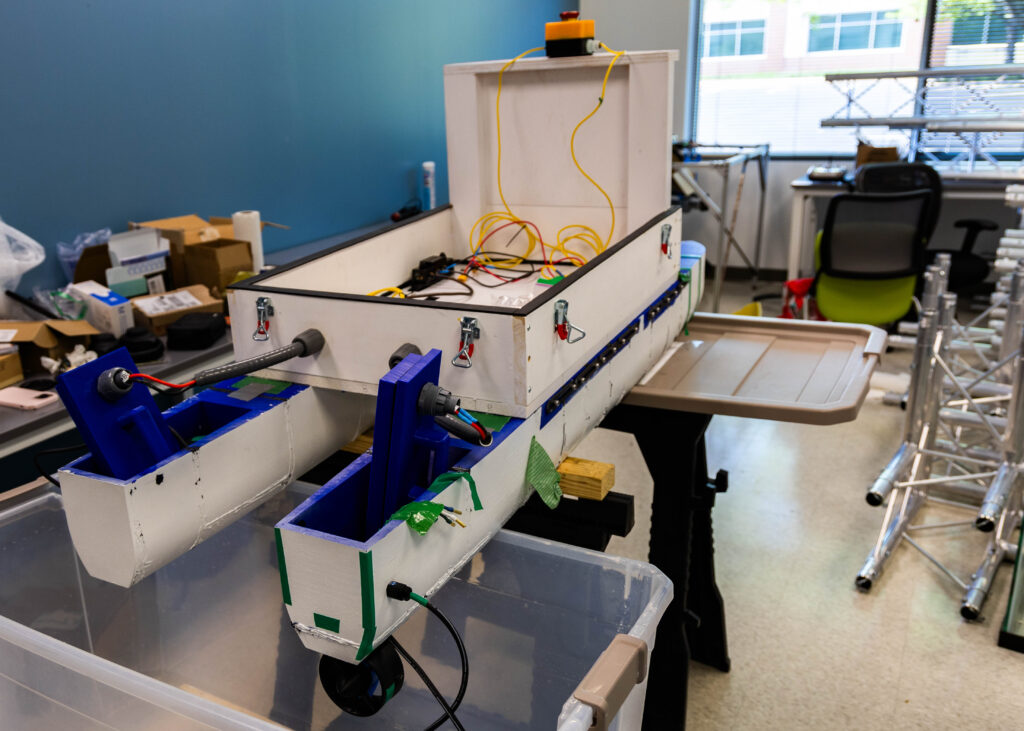
Demihull Design
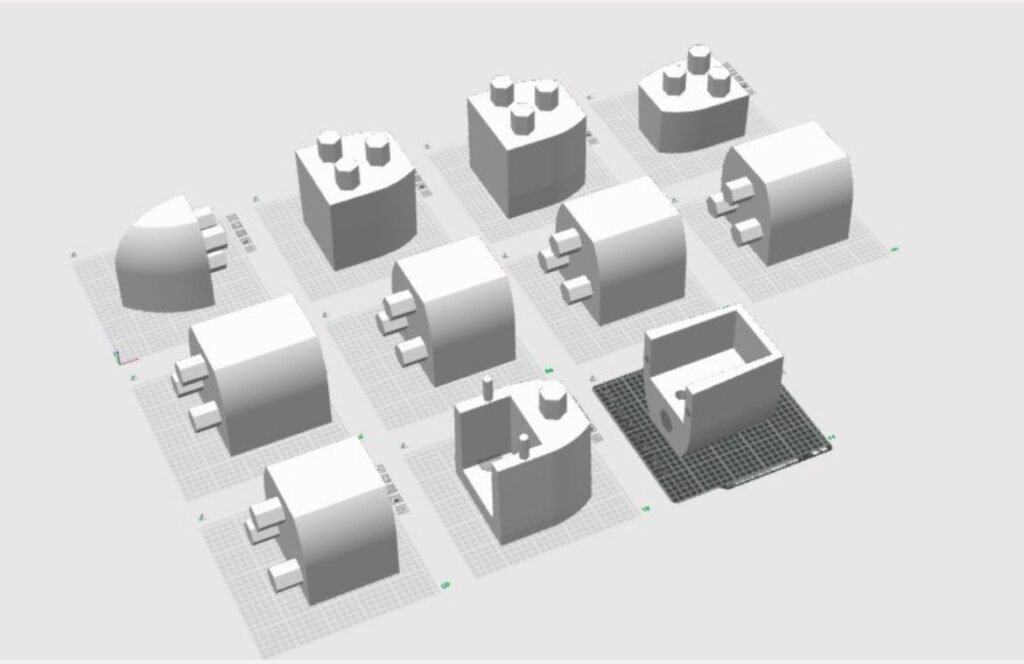
The hulls were designed using Autodesk Inventor and 3D printed using PETG filament. Printing was done in sections sized to the capacity of a Bamboo P1s printer. The sections were then glued together, with silicone sealant across open gaps to enhance water resistance. The demihull dimensions are 60 inches for the total length, 6 inches for the beam, and 6 inches for the depth. They feature bulkheads to support structural integrity and to help compartmentalize the demihull in case of flooding. To verify the design process, the team used CAD for visualization and fabrication. To verify the model’s buoyancy and stability, the team used Orca3D, which is a marine design plug-in for the Rhino3D software commonly used in naval architecture.
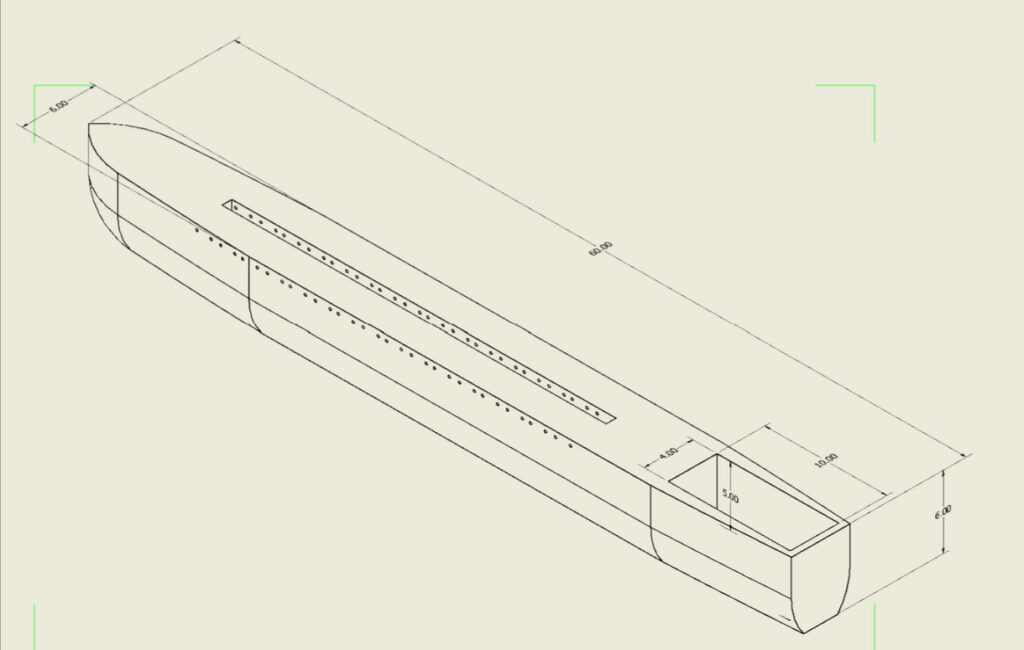
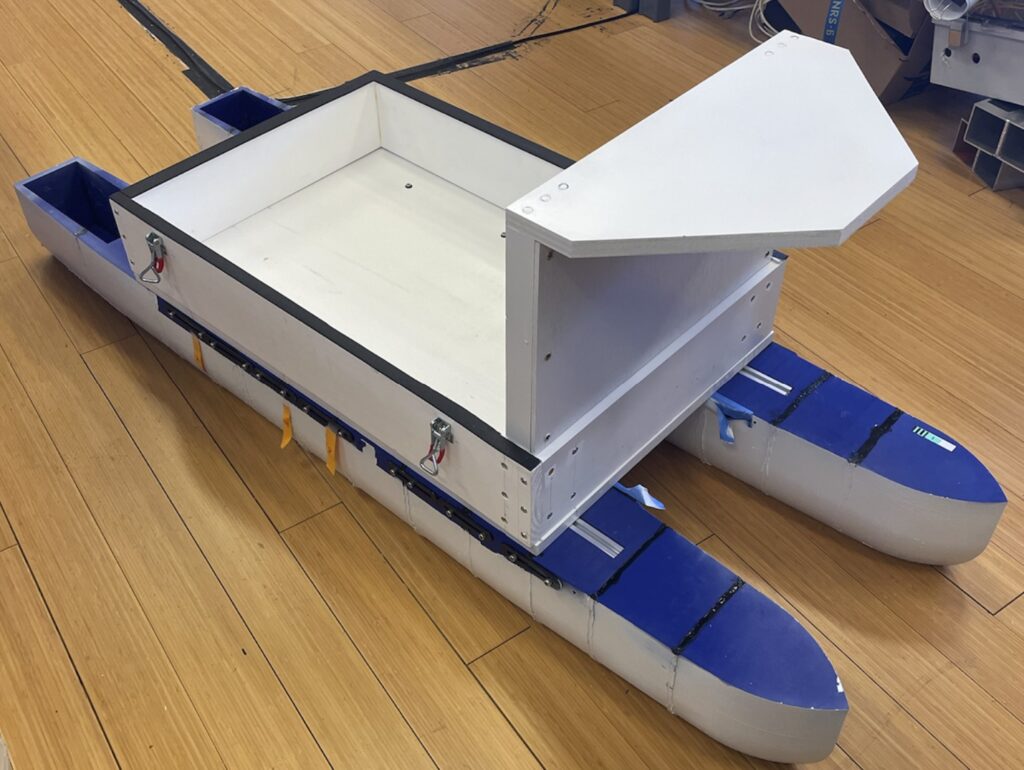
Electrical Schematic
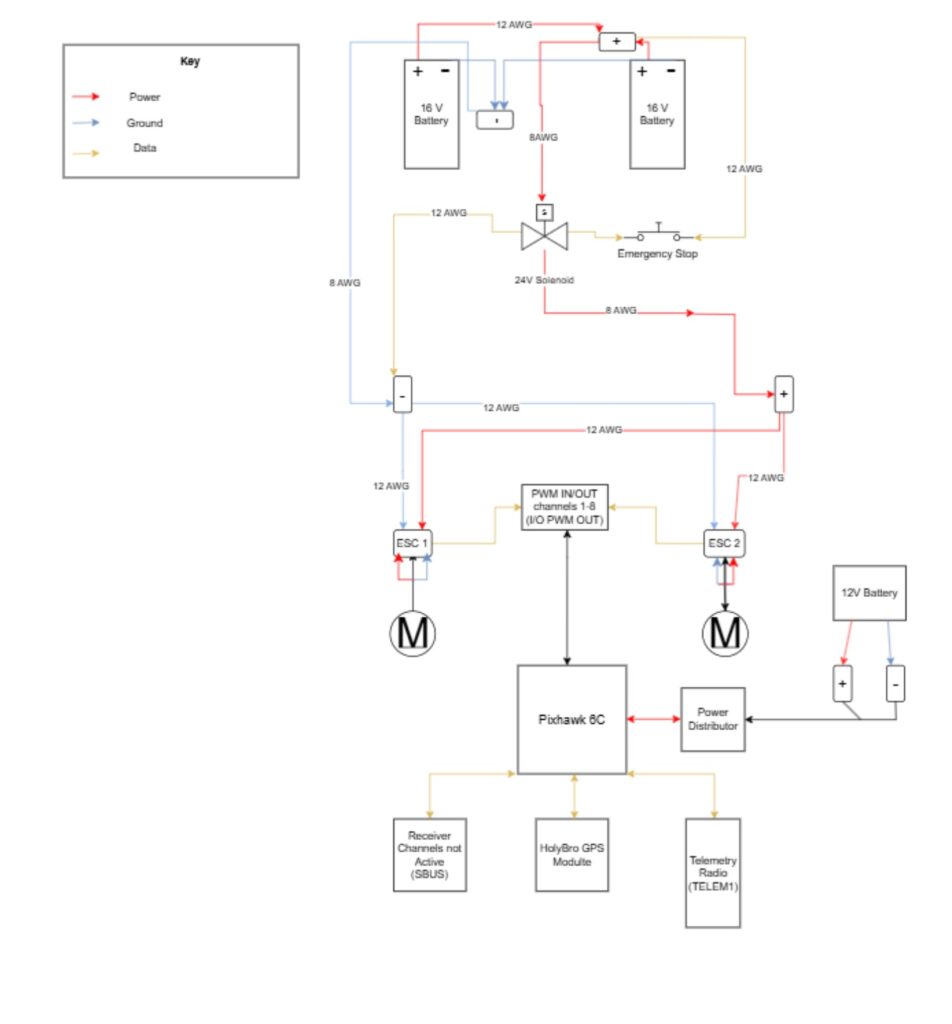
The electrical system was inspired by what the team used at the 2024 RobotX Challenge and what the spring 2024 Promoting Electrical Propulsion Capstone Team used for their capstone project. This boat’s electrical system is designed for safety, reliability, and future flexibility. It includes an emergency stop button that immediately cuts power to the motors if needed, similar to systems used in previous competitions. All components, including the solenoid and wiring, were chosen to handle more than the expected electrical load and will be tested thoroughly before water trials. A 12V battery powers the system, with voltage converters ensuring safe and adequate levels for each component. The boat is controlled by a Pixhawk 6C flight controller, chosen for its reliability and adaptability. It connects to a GPS and telemetry radio for real-time tracking and communication. A switch allows easy toggling between manual (RC) and autonomous control modes, with the manual mode already tested.
Lid Model with Custom Thermoplastic Polyurethane (TPU) Gasket
To prevent any water splashing into the cavity that holds the ESCs, lids were designed in Autodesk Inventor. In the final design, it should be noted that there is a one inch hole on the top surface to accommodate for wires connecting from the ESC to the main superstructure of the vessel. A custom-made gasket was 3D printed out of flexible Overture TPU filament to ensure a flush fit seal with the lids.
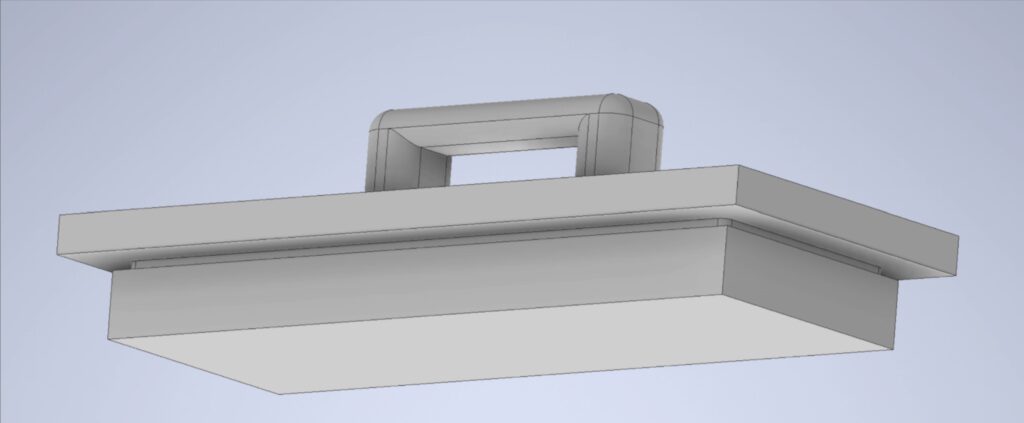
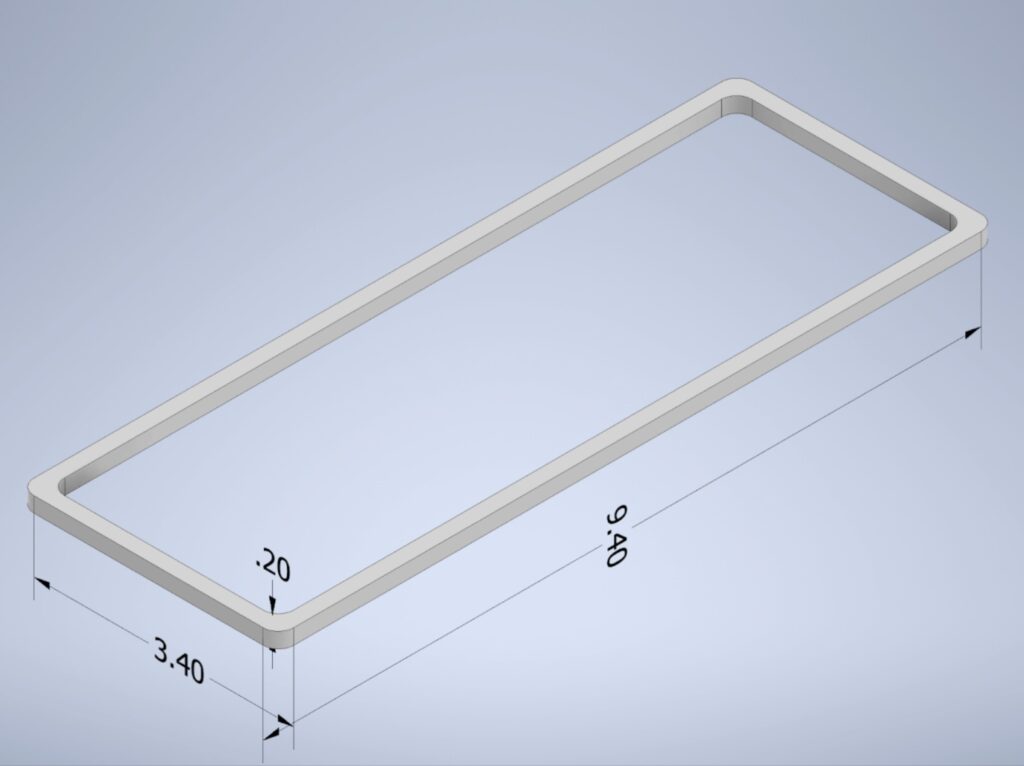
Tolerances proved to be a challenge as the first printed lid was slightly deformed, causing an uneven edge where the TPU gasket would fit. Numerous test pieces and versions of the TPU gasket were printed to get a perfect sealed fit, thus there are two different versions of the printed gaskets that go with associated lids. A flathead screwdriver is used to push in the edges of the TPU gasket to create a strong, waterproof seal.
Future Work
The Occoquan Otters made it far to ensure the RoboBoat floats and has remote-controlled capabilities. For the future, the team can strengthen the software side and most likely implement LiDAR technology to ensure the boat is capable of object detection. Certain tasks prescribed by RoboBoat competition rules require shape and color detection. In the future, performance at competition can be improved by emphasizing the software aspects of this project, including implementation of LiDAR technology and stereovision to support object detection and avoidance.

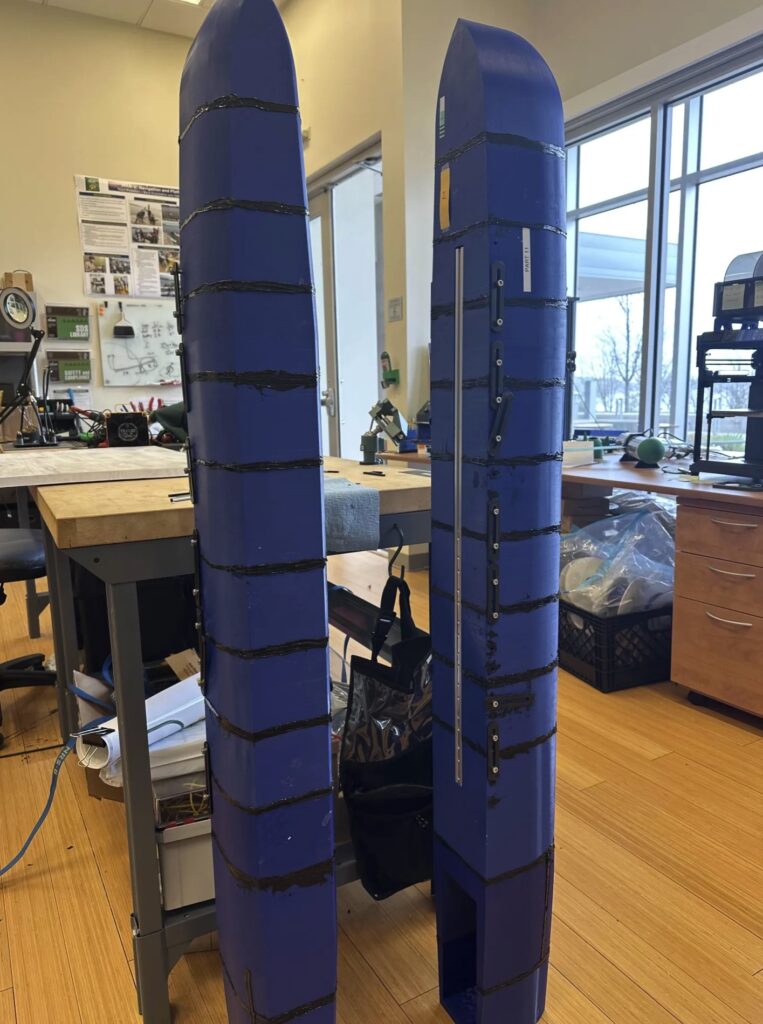

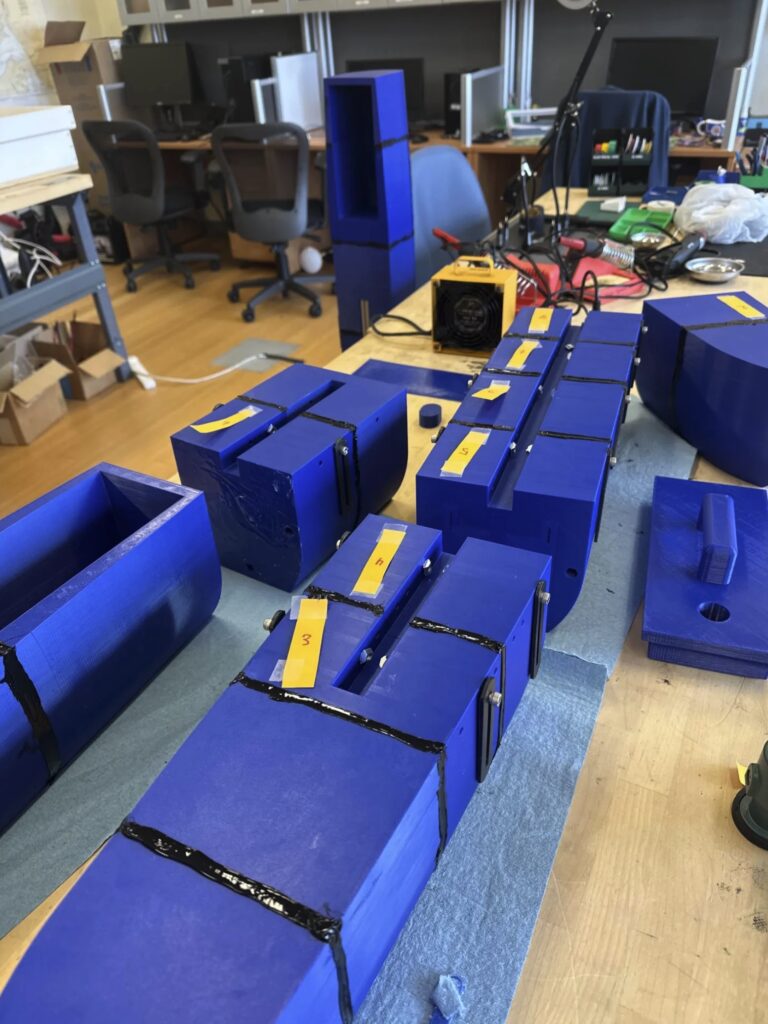
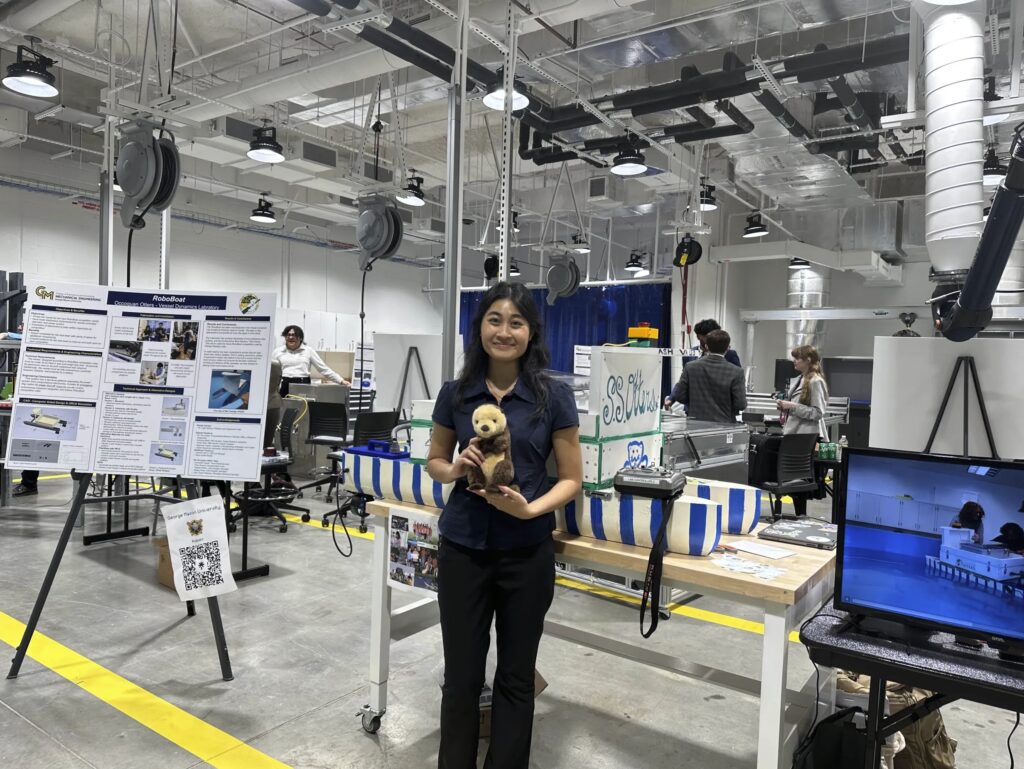
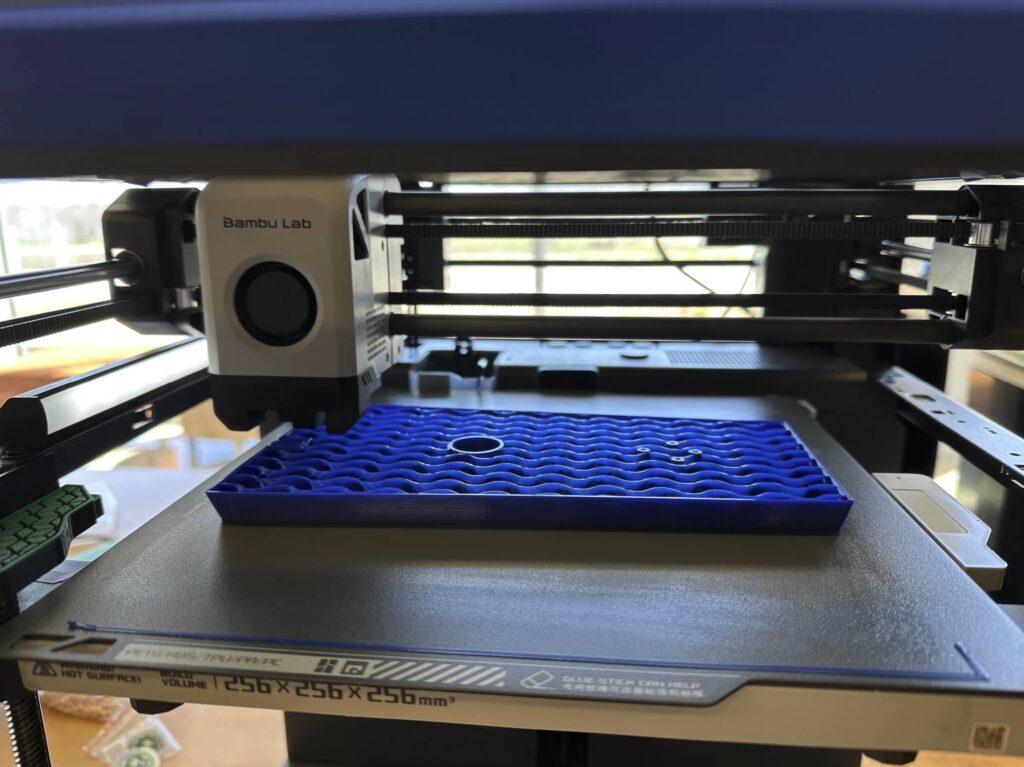
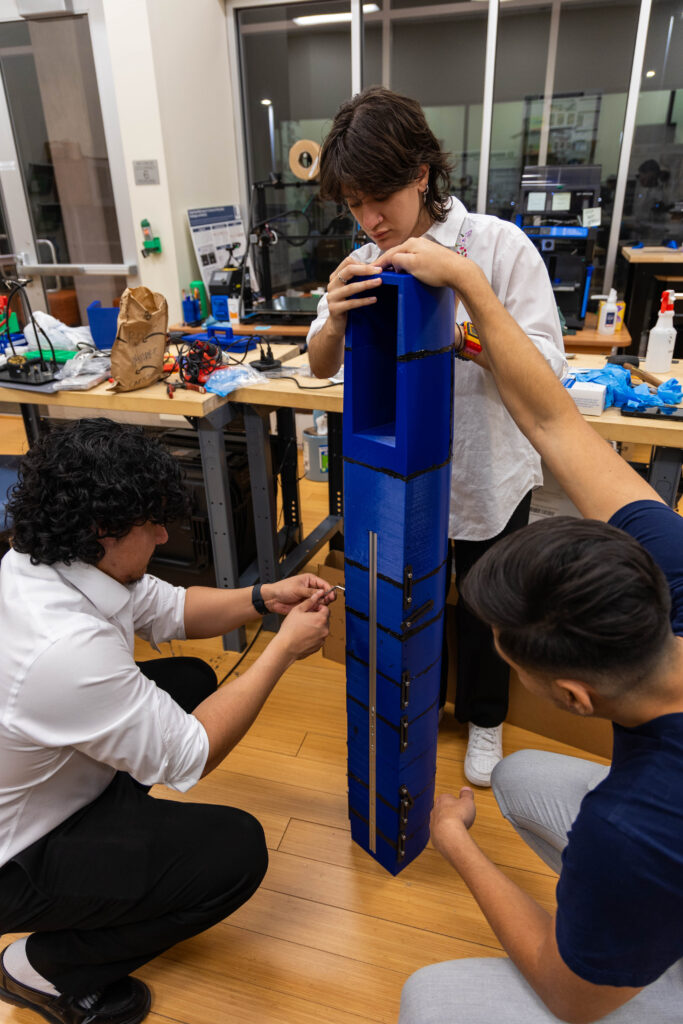

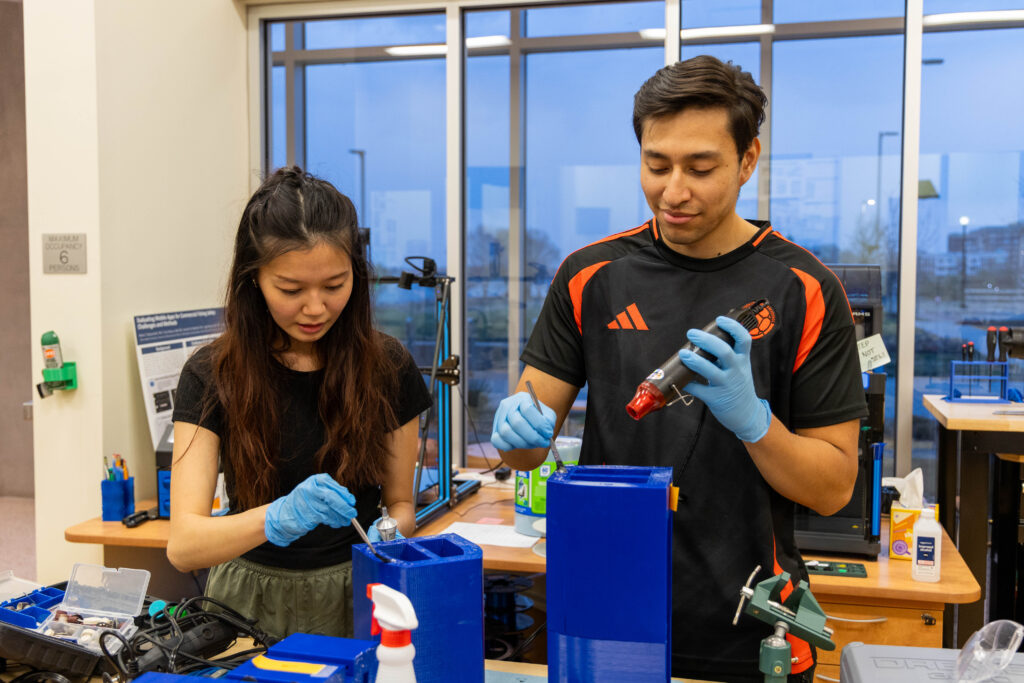